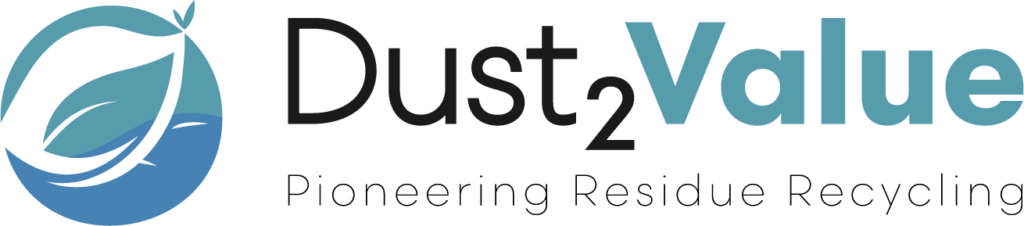
Electric Arc Furnaces recycle galvanized steel scrap, producing hazardous Electric Arc Furnace Dust (EAFD) as a by-product. Dust2Value’s innovative process converts this waste into valuable resources, recovering zinc concentrate and secondary-grade Direct Reduced Iron (DRI) for metal production. Our robust process design efficiently utilizes hydrogen for reduction, handles various types of input materials, and requires no agglomeration. This versatility makes it a promising future recovery method for EAFD and other zinc-containing industrial waste materials, paving the way for more sustainable metal recycling practices
The EAFD Recycling Concept for a Sustainable Future
More details about the Dust2Value program arriving soon
The Dust2Value project was set up to demonstrate the feasibility to decarbonize the state-of-the-art Waelz process to recover zinc from steelmaking waste streams, in particular electric arc furnace dust (EAFD). The Dust2Value process uses green hydrogen to distil zinc by reducing zinc oxide to metal zinc vapor. The novel concept allows in-situ reoxidation with water vapor, forming fine zinc oxide particles which exit the furnace via the off-gas stream. These particles are recovered in bag-house filters and serve as secondary zinc concentrate. Additionally, the process produces secondary-grade DRI (Direct Reduced Iron) reusable in EAF steelmaking. The innovation results from the extensive background knowledge and detailed insights from basic research which have led to an optimized process design that achieves exceptionally high extraction rates for zinc and a high degree of metallization for iron.
Dust2Value recovers all valuables from the steelmaking wastes, resulting in a significant higher resource efficiency
CO2 emissions from zinc oxide production within the Waelz process is reduced to net zero.
The process design allows to recover heat required for reduction and evaporation of zinc within the process